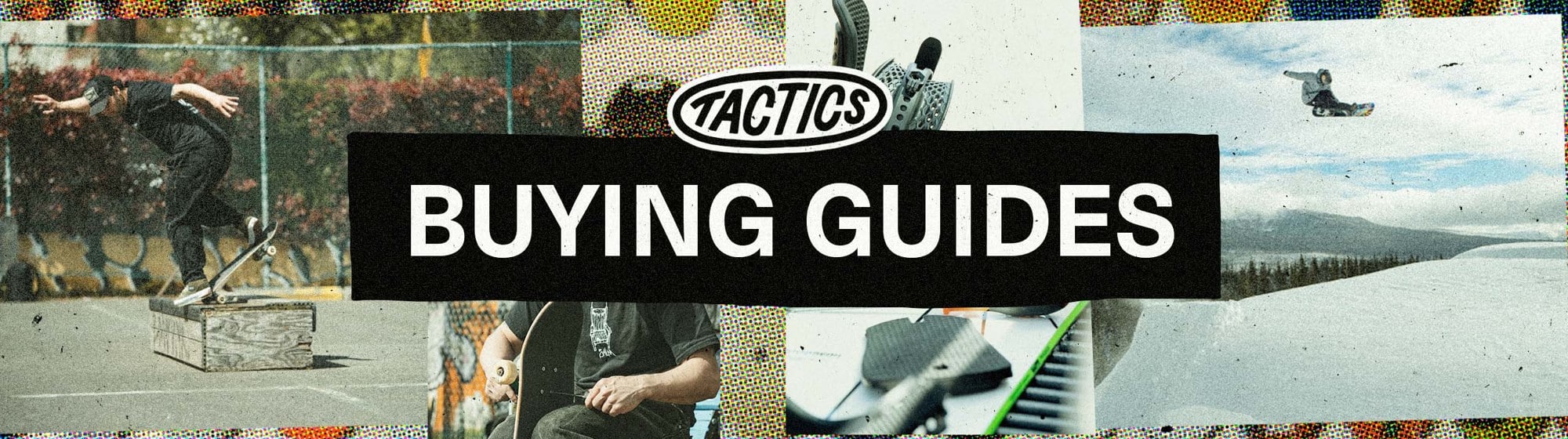
We've put together the ultimate guide to figuring out the intricate worlds of skateboarding and snowboarding. Whether you're setting up your first board, buying a gift, or just curious about some tech, we've got you covered in learning the ins and outs to snag the right gear for you.
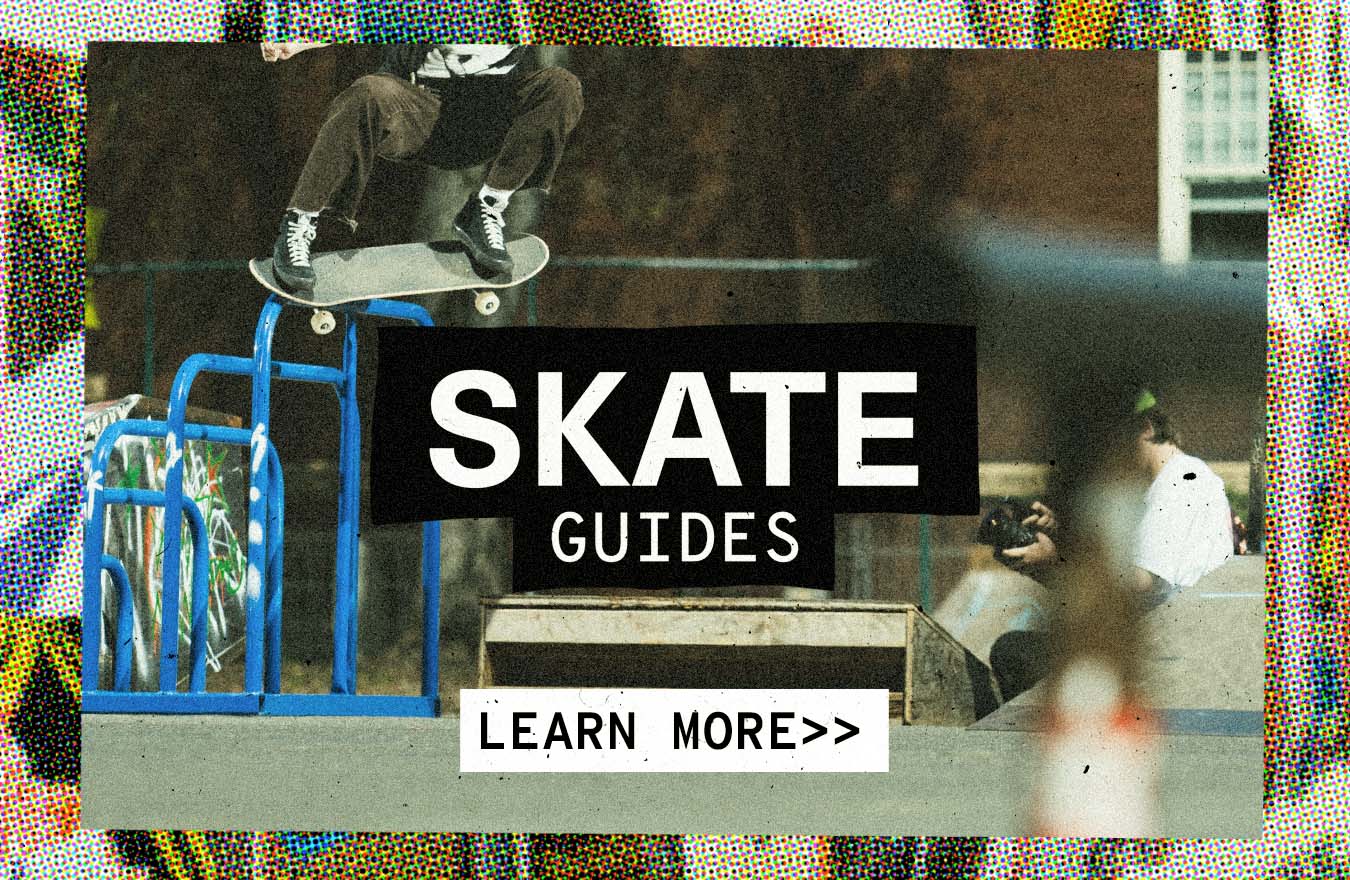
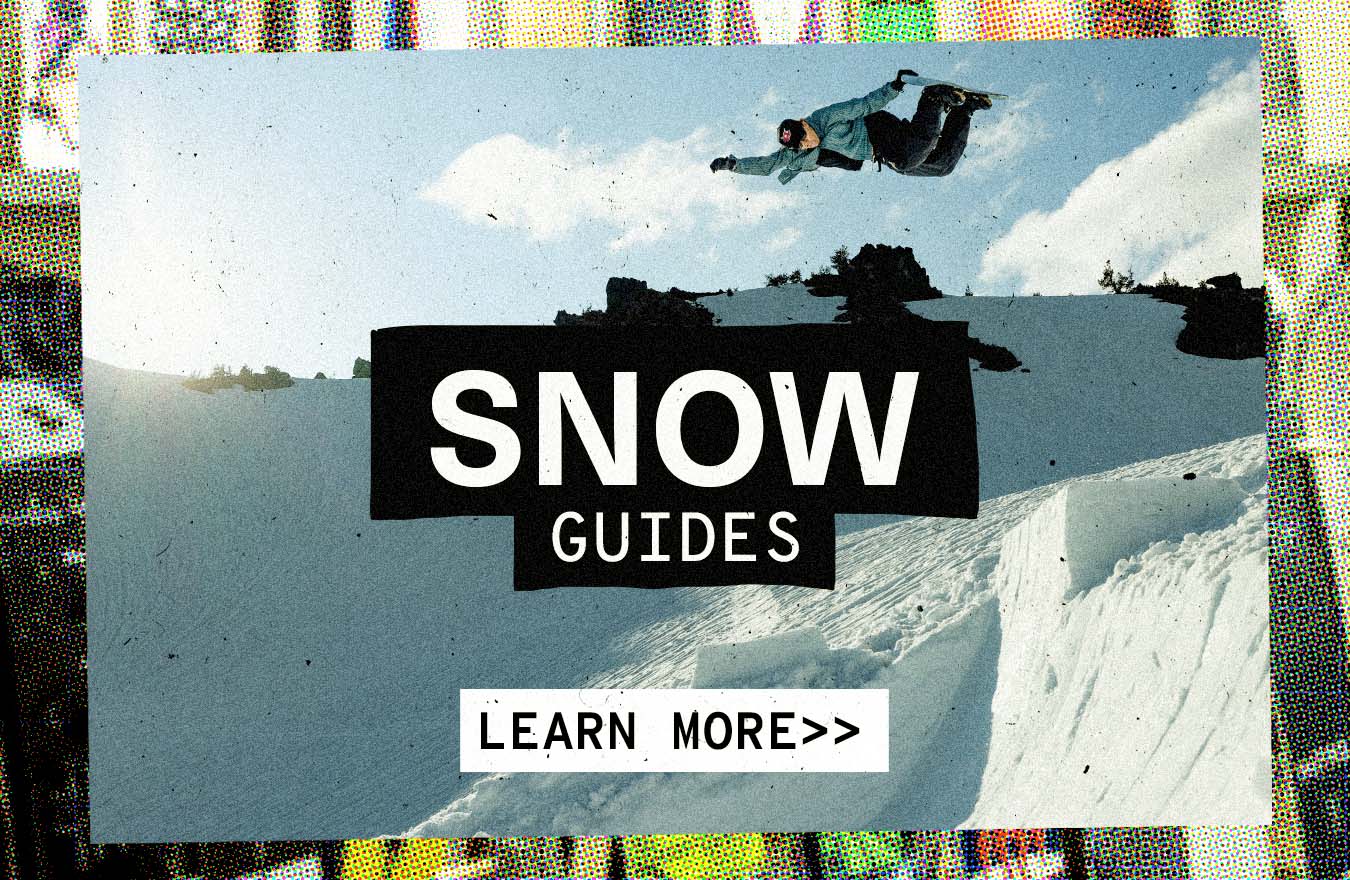